Rhys Faultless
About
I'm a Staff System Engineer at Clearpath Robotics. Most of my time is spent on system design, though I am also a generalist that performs tasks in disciplines like: mechanical, electrical, robot software, web development, and configuration management. I use many repositories for storing data, like GitHub, Trello, Jira, Confluence, and Google Docs. I hope that this site will allow me to create an index of all this data, and make it sharable where possible. I will attempt to provide links and references for further reading, but overall this site should not be considered a complete knowledge base for the related subjects.
My Experience
Click to download a PDF copy of my resume
2023 - Present
Staff System Engineer, Clearpath Robotics
I have been designing the Husky A300, a wheelchair sized robot, that can carry 100 kg of payload at 2 m/s, (220 lbs at 4.5 mph). I created the Systems Engineering documentation for this project, including;
- Concept of Operations,
- Architecture block diagrams,
- Technical requirements and related tests,
- Researching and bench testing components like the batteries,
- Configuration management,
- Defining system interfaces, for modularity of SKUs,
- Costing.
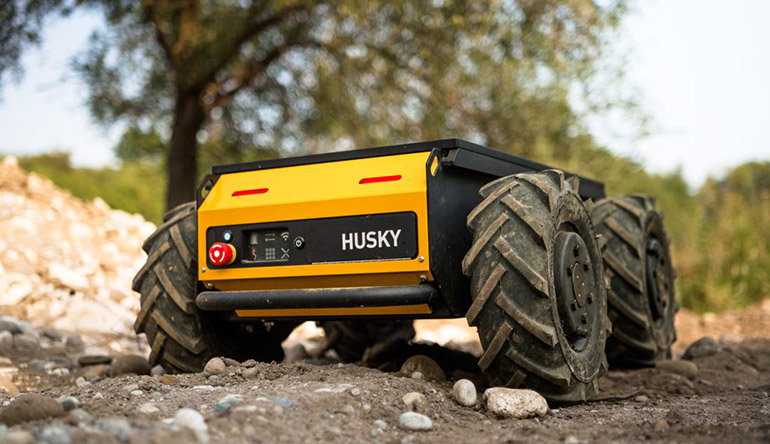
I also performed many Mechanical Design and Engineering tasks.
- SolidWorks lead designer,
- Chassis design,
- Cable and busbar routings,
- Power system layout, with contactors, fusing, and connectors,
Unrelated the the Husky A300 project; my progression from Engineer ⟶ Senior Engineer ⟶ Staff Engineer has been aligned with Will Larson's description in Staff Engineer. I continue to perform many of the same tasks as before, but I spend more of my time writing documentation, creating designer tooling, and developing architecture for robots.
2021 - 2023
Senior System Engineer, Clearpath Robotics
Some of the robotics projects I worked on in this time were; the Husky Observer, and a retrofitted Polaris GEM to be controlled with ROS. My tasks on these projects included: requirements definition, power budgets, wiring diagrams, cable drawings, mechanical drawings, building robots, testing the systems, and commissioning them with end customers.
I developed PACS—Platform Attachment Configuration System—which is used for integrating robots. The outcome seems simplistic, but the development process required input from multiple stakeholders, and support for legacy products.
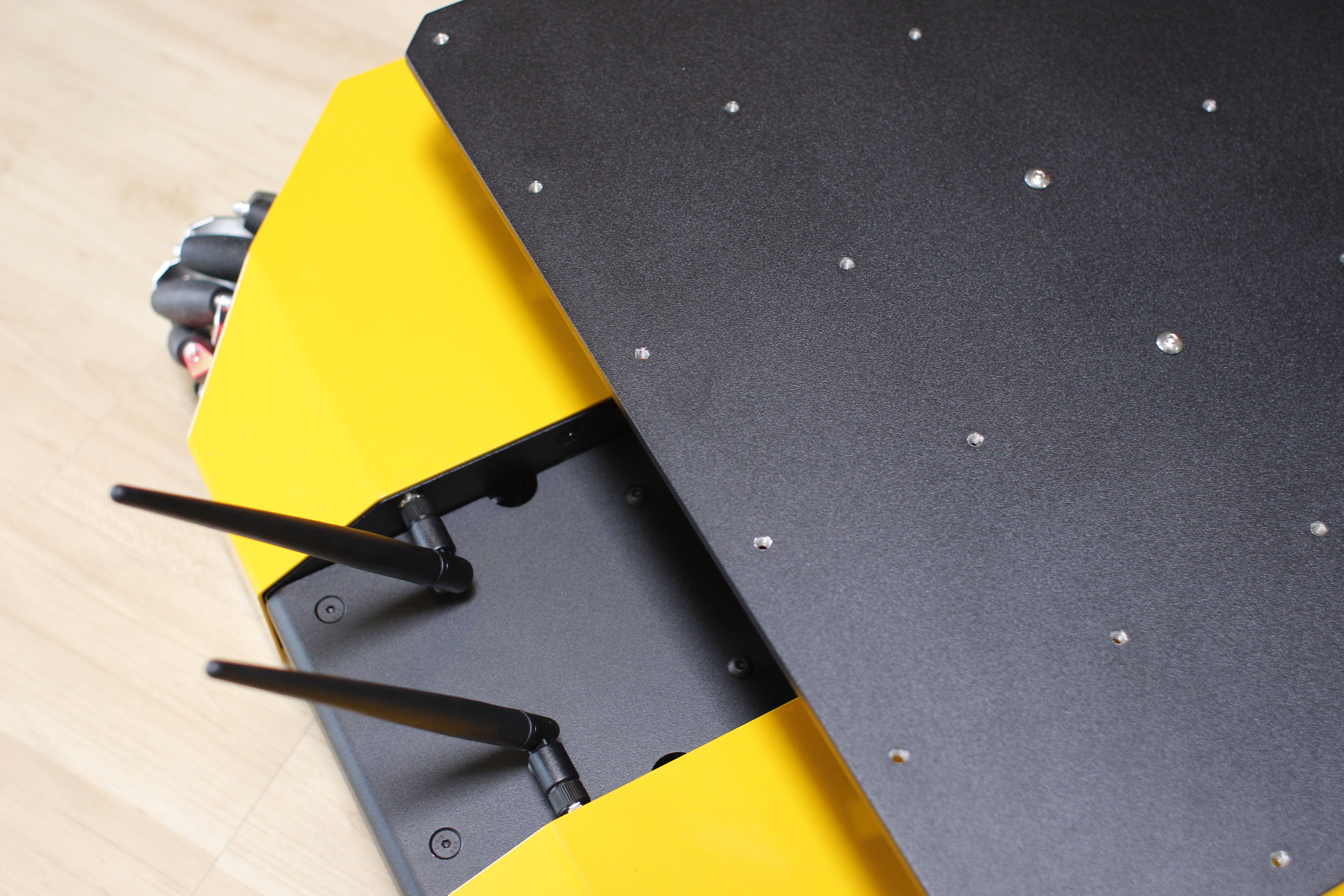
I also researched website documentation tools, and set up docs.clearpathrobotics.com to simplify the process of maintaining Clearpath's public documentation. Note that much of the website's documentation was written by my colleagues, as seen in the GitHub repository's collaborators area.
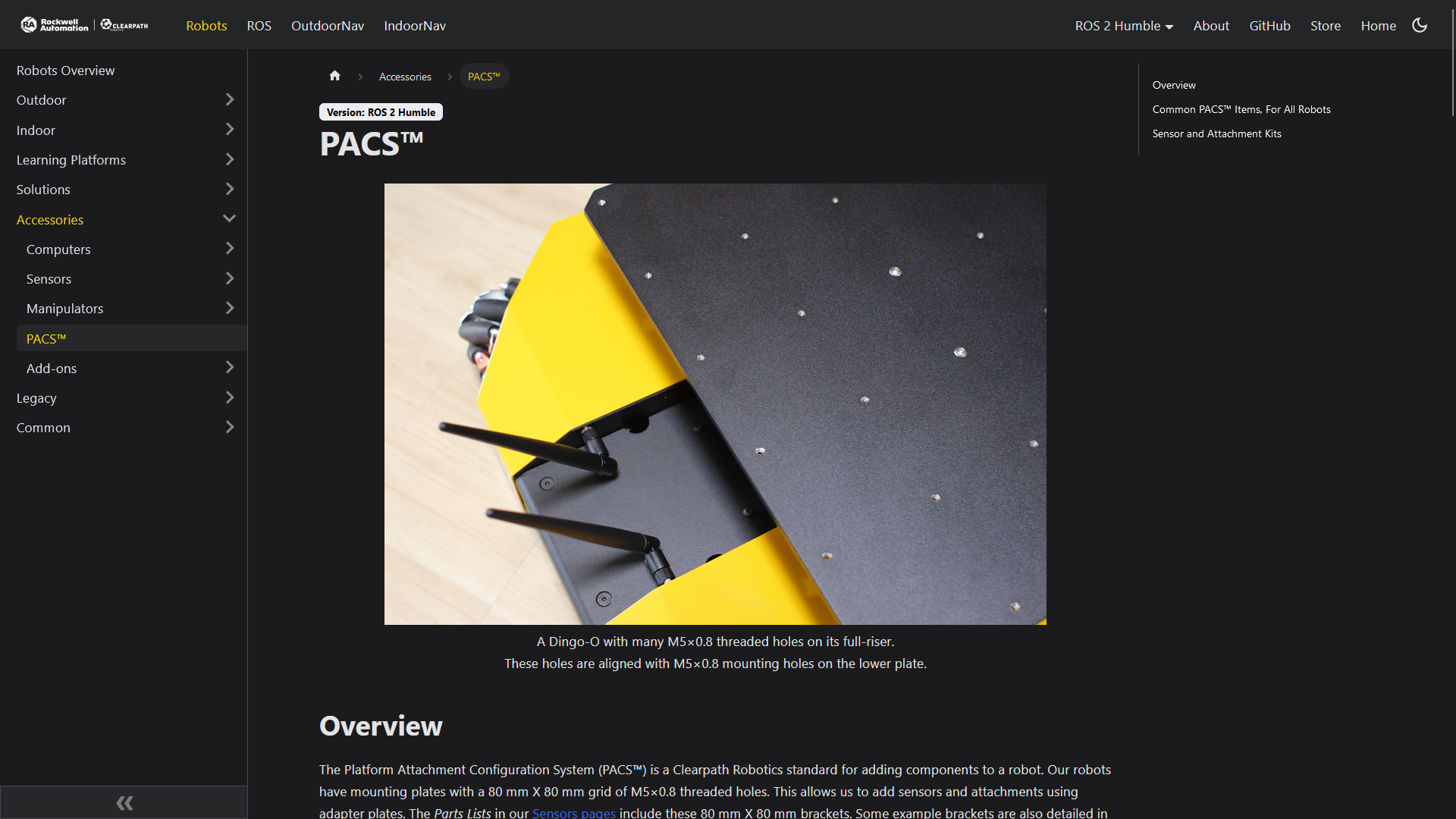
2020 - 2021
Senior Mechanical Engineer, Clearpath Robotics
This was the height of COVID-19 lockdowns, so lots of work became remote, with engineers performing modular / discrete tasks. During this time, I integrated several robots, such as this Boxer UGV with RFID sensors. Some robot integrations were simple like the Boxer, but others were more complex, with many sensors and manipulators.
I also defined the system requirements, and drafted concepts for the TurtleBot 4. This was a collaboration between Clearpath Robotics, Open Robotics, and iRobot.
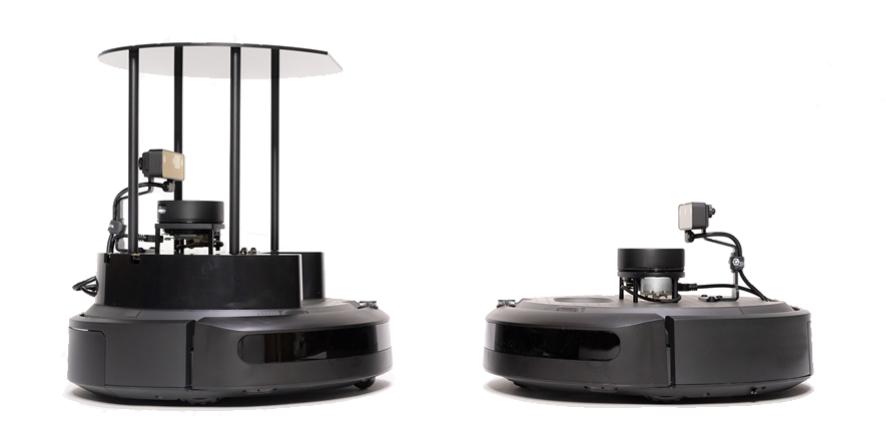
2019
Professional Engineer Designation (P.Eng.), Professional Engineers Ontario
License Number 100218635
2018 - 2020
Mechanical Designer, Clearpath Robotics
My initial work at Clearpath Robotics was the mechanical design of the Moose UGV. I used SolidWorks to review robot assemblies, model brackets, and design rotating components.
Other projects during this time included mechanical tasks related to: drivetrain design and analyis, waterproofing electronics, and cooling electronics with heatsinks or forced convection.
Though the role was defined as Mechanical Designer, I wired robots, designed and built cables, and configured sensors and computers. I also designed a PCBA with an Atmel microcontroller for the Heron USV's Water Sampler. The new PCBA was to simplify the manufacturing of the legacy Water Sampler product from 2016. I also updated the ROS driver for the Water Sampler to be compatable with ROS Melodic.
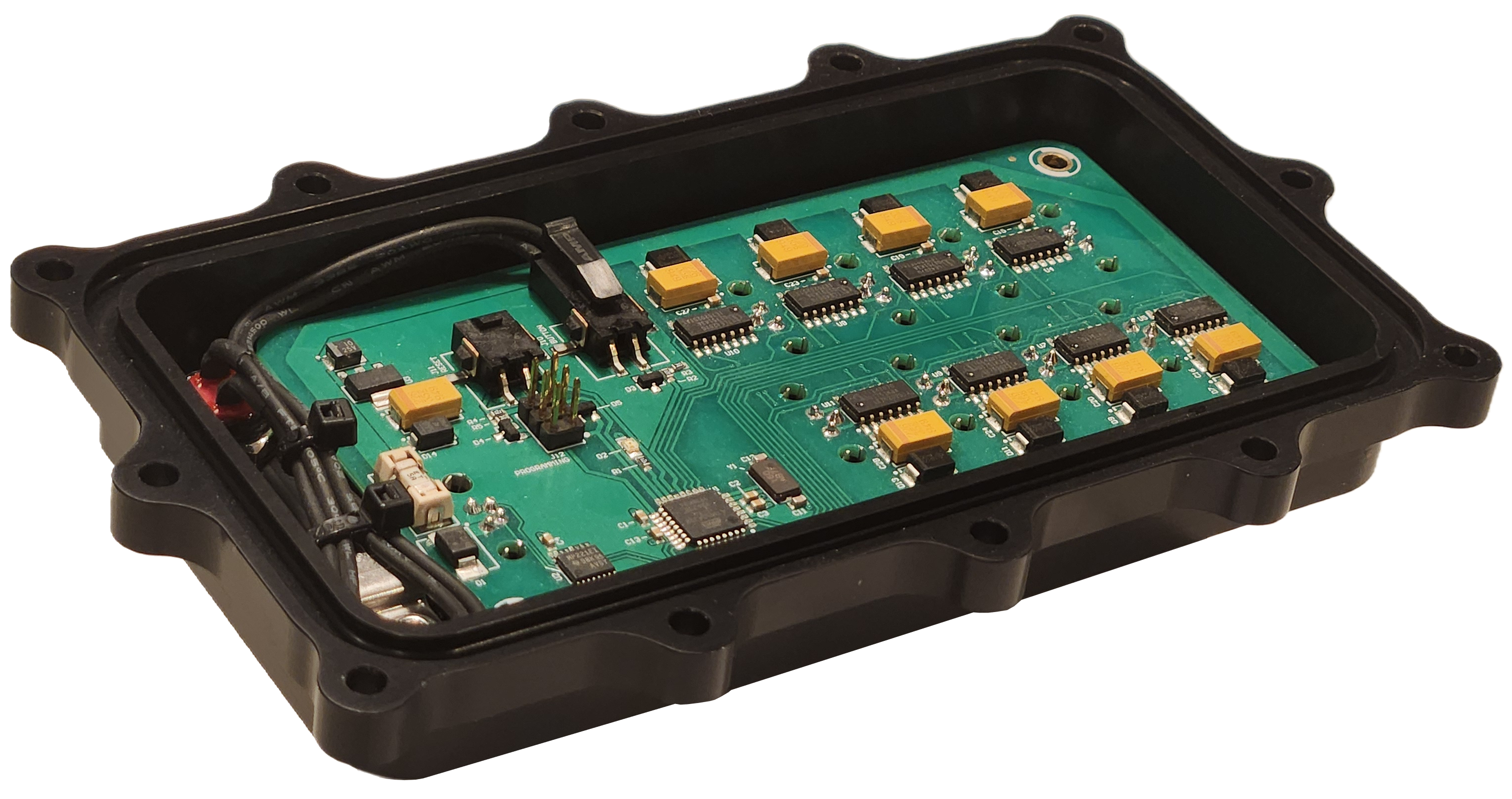
2015 - 2018
Physical Architect, GDLS-C
I was the main CAD maintainer for several vehicle variants being developed for the LAV 700.
This included: holding design reviews, creating concepts, defining space claims, reviewing subsystem designers' assmemblies with reference to the entire vehicle, and assessing build issues on the production line.
I also did mechanical design and engineering work for some subsystems, like the mirrors.
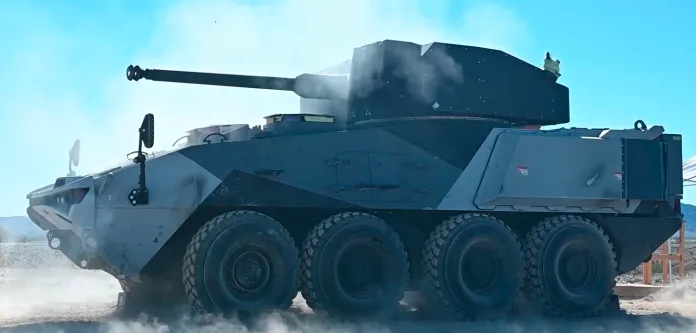
2015
Designer, GDLS-C
I updated drawings, CAD models, and assemblies with Siemens NX and Teamcenter.
I also designed the LAV 6's stowage subsystem, which stored troops's kit and supplies. This included brackets, hinged covers, and fabric tie down straps.
2010 - 2014
Bachelor of Engineering, McMaster University
I studied mechanical engineering, with a focus on fluid dynamics.